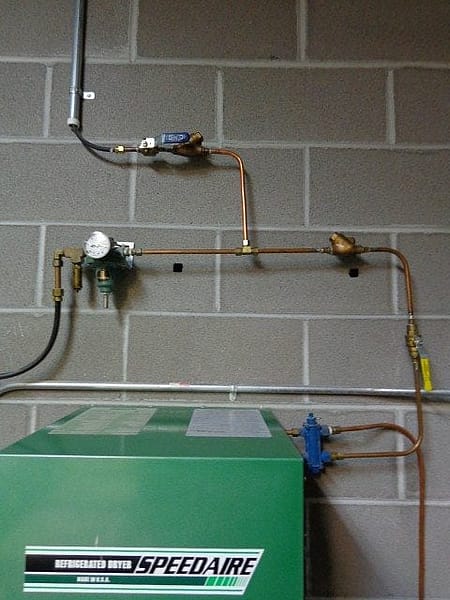
Air Compressor Efficiency Improvement: Facilites Compressor part 2
Our big Facilities air compressor has capacity control by way of what the manufacturer calls a poppet valve. As the compressor builds pressure to its setpoint, a regulator applies pressure on the poppet, restricting the amount of air that enters the compressor (the less air the compressor is pumping, the less energy it’s using.) In setting up the capacity control, I closed the valve isolating the distribution piping from the compressor, preventing it from pumping any air.
While performing this procedure, I noticed that the power consumption when the valve was closed was not much different than consumption when the valve was open, implying that there was very little useful work being done. Most of the power this machine was using was simply going into turning its components, not actually moving much air. If you’re going to use a bunch of energy making machine parts go round and round, you might as well get some work done, right? The humidification systems supplied by this machine did not require nearly the volume of air this big machine was able to produce. I needed to find more work for it to do.
Our HVAC control system is a hybrid of digital and pneumatic technology. Each of our galleries was built with its own control air compressor installed. Fortunately for me the control panels for our humidifiers were located near the panels for our HVAC system controls, so a little bit of creative piping enabled me to connect control air to the Facilities compressor and take the smaller control compressors out of service. Also, the carpentry shop is located directly above the Facilities boiler room, so piping to that area was easily accomplished, putting the compressed air load for the carpenter’s tools onto the big compressor as well. This eliminated approximately six horsepower of motor load from the small compressors. When all this work was done, there was still plenty of available capacity from the Facilities compressor, but the story doesn’t end here…
Written By
Phil Anthony
Phil Anthony is the Operating Engineer at the Buffalo Bill Center of the West. He has been in the HVAC-R service industry for over 30 years (fifteen of them at the Center.) Phil holds journeyman certificates through the City and County of Denver as a steamfitter and a refrigeration technician, and a low-voltage electrical technician’s license with the state of Wyoming. An artist, poet, musician (sort of,) and avid outdoorsman, Phil has been called "a true renaissance man."