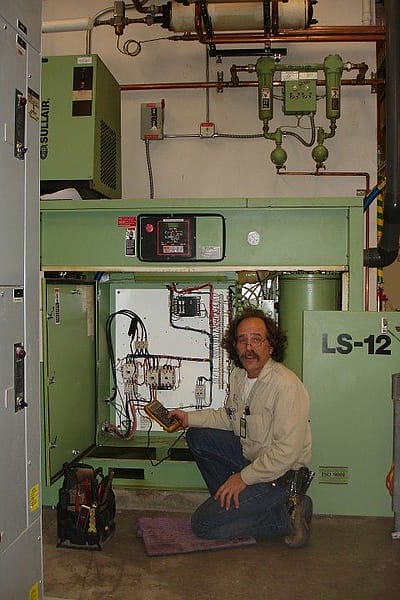
Air Cooled to Water Cooled Conversion: Facilities Air Compressor Part 1
In 2000 – 2002, the Center built its most recent additions to the building, the Facilities wing and the Draper Natural History Museum. As part of the design, engineers incorporated atomizer humidifiers (in contrast to the steam humidification systems in older parts of the building). Compressed air for the new humidification systems was provided by a Sullair 50 horsepower air-cooled screw compressor located in the new boiler room of the Facilities wing. We encountered a design problem with our new mechanical system within a week after the compressor was commissioned. The offices above the boiler room, which had been maintaining a comfortable temperature for months before the compressor was started, were warming up to uncomfortable (80 degrees F) temperatures.
Of course I checked the air handling system and related components to be sure they were operating normally. Everything seemed fine. But I did notice that the boiler room, which uses outside air to stay cool, had gone from around 90 degrees (the time of year was late summer) to well over 100 after the compressor came on line. The heat generated by the compressor, being discharged directly into the boiler room, was acting like “in floor” heat for the spaces above.
I did a little research, uncovering the fact that the compressor manufacturer built a water-cooled version of the compressor, and our engineering firm agreed to share the cost to perform an air-cooled to water-cooled conversion of our machine. The heat exchangers were piped into our chilled water system, air and compressor fluid lines were routed, and behold! Our air conditioning problems in the upstairs offices went away.
In a facility whose chiller capacity might already be borderline, this solution would not have worked. But in our case, practically every new system in the Facilities wing, including our cooling system, was over-engineered (more on this topic another day).
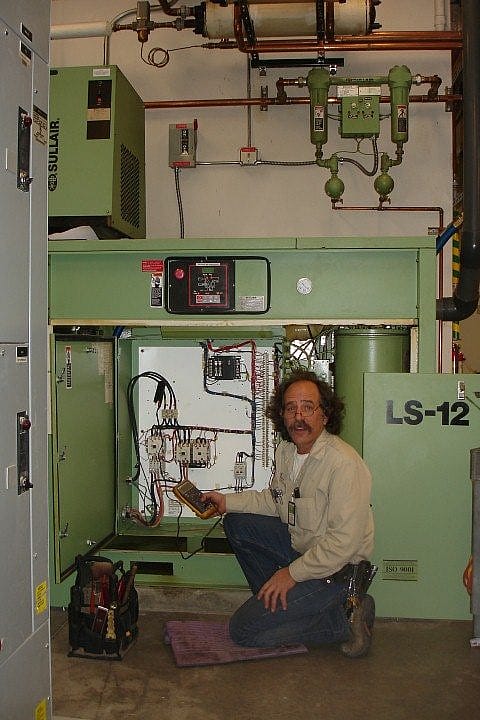
Written By
Phil Anthony
Phil Anthony is the Operating Engineer at the Buffalo Bill Center of the West. He has been in the HVAC-R service industry for over 30 years (fifteen of them at the Center.) Phil holds journeyman certificates through the City and County of Denver as a steamfitter and a refrigeration technician, and a low-voltage electrical technician’s license with the state of Wyoming. An artist, poet, musician (sort of,) and avid outdoorsman, Phil has been called "a true renaissance man."