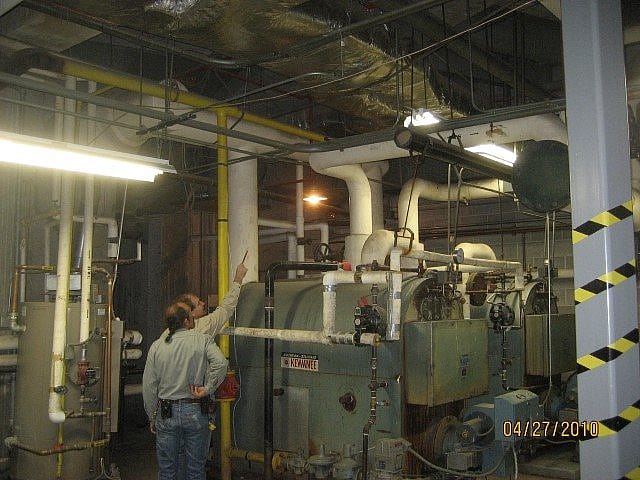
SEP-ARRA: Your Tax Dollars at Work
It was autumn of 2009, and the news was not good…
The old steam boilers which provided heat and, indirectly, humidification for our 1967 building addition (the Whitney Museum, Buffalo Bill Museum, Center hub, and Special Exhibits/Library areas) were dying of “cancer of the boilerplate”—they were rusting out and beginning to leak. Meanwhile, on the other end of the building, the chiller providing cooling for the Cody Firearms Museum was worn out and required a rebuild. A huge capital investment seemed inevitable, at a time when the museum’s budget was already stretched.
But out of darkness a faint glimmer of hope…
Lynn Houze, assistant curator for the Buffalo Bill Museum at the time, came to me with a news release from the Wyoming Business Council. It was an invitation to submit grant applications for a pool of money provided by the federal government to apply toward energy saving building retrofits, the State Energy Program–American Recovery and Renewal Act or SEP-ARRA. It seemed destined: we could not pass up such an opportunity!
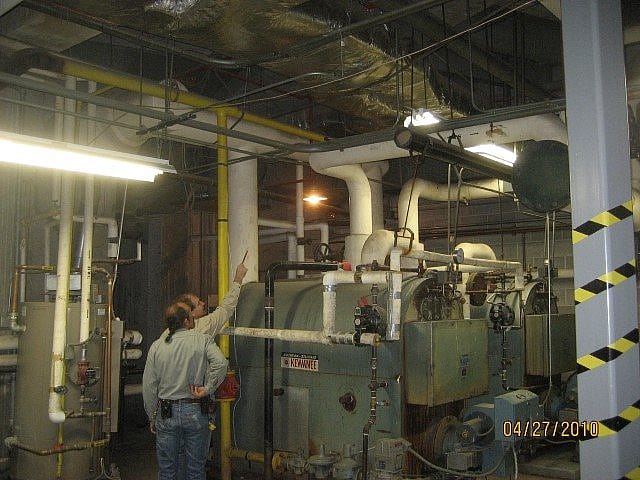
We were operating under a deadline, with only about ten days before applications were due, but I wanted to make the best pitch possible, so, with the approval of my supervisor, I called in a team from CTA Architects to help us recommend cost-effective retrofits. CTA was a natural choice, as the firm had been involved in the design in 1999 of our Central Plant, and in creating a document titled the “Engineered Systems Master Plan,” which spelled out a vision for the future of our building’s mechanical systems. Here was our opportunity to apply the vision around which the Central Plant had been built!
CTA did a masterful job of describing various projects and estimating energy savings (a requirement of the grant.) Bruce Eldredge, our Executive Director, approved the 10 percent in matching funds we were expected to provide under the terms of the grant, and through the wonders of modern postal delivery our application arrived at the Wyoming Business Council at least six hours under the deadline! Better yet, it was approved! We received (including our own matching funds) more than three quarters of a million bucks toward retrofits to our building!
You’re welcome to contact me for the technical details of the work done, but…
Here’s the short version…
- The Central Plant had been designed to carry the heating load for the entire facility, and while it was originally expected that we would need to install an additional chiller to carry the cooling load, we calculated that the existing chiller could probably do the job.
- Piping and related components were added to the 1967 section to provide heat and eliminate the need for new boilers there; new piping also connected the Facilities chiller to the Cody Firearms Museum, eliminating the need for chiller repairs in that section of the building.
- A modern humidification system was installed on each of the air handlers formerly dependent on the old steam boilers (this relates back to previous blog posts about our Facilities air compressor, part 1 and part 2).
- Insulation was added in areas identified as being inadequate.
- And on top of all that, we had grant money left over to lamp the Whitney Museum with LED lighting.
But wait—it gets better!
As a condition of the grant, I was required to report monthly on our energy consumption to the Wyoming Business Council’s State Energy Office. When they saw our results in reduction of energy use, we were invited to apply for (and subsequently received) another $25,000 in grant money which we used to lamp all our other galleries (excluding the Draper Natural History Museum) with LED lighting!
As a taxpayer, I feel this was a worthwhile investment. Between 2010 when the grant work began, and 2012 when it was completed, electrical consumption was reduced by more than 15 percent, and natural gas consumption reduced by more than 23 percent!
Written By
Phil Anthony
Phil Anthony is the Operating Engineer at the Buffalo Bill Center of the West. He has been in the HVAC-R service industry for over 30 years (fifteen of them at the Center.) Phil holds journeyman certificates through the City and County of Denver as a steamfitter and a refrigeration technician, and a low-voltage electrical technician’s license with the state of Wyoming. An artist, poet, musician (sort of,) and avid outdoorsman, Phil has been called "a true renaissance man."